
Common bad phenomena and treatment methods of pulse laser customers on site
Published:
2019-12-01
Common bad phenomena and treatment methods of pulse laser customers on site
1. There is no laser output suddenly during the working process, and the remarking software displays "IPG system fault"
Answer: 1) the processing material does not belong to high reverse material: change the laser to another normal marking table for testing. If there is still no light output, please contact the after-sales personnel of Ruike; if there is light output, please check the original marking table.
2) the processing material belongs to the high anti-material: the laser is restarted and marked in the way of focusing. If there is light output, mark in the way of focusing; if there is still no light output, replace the laser with another machine which is confirmed to be normal for marking test in the way of focusing. If there is still no light output, please contact the after-sales personnel of Ruike and feedback this information to the after-sales personnel.
2. There is no laser output suddenly during the working process. The remarking software displays "IPG system fault - over temperature"
Answer: 1) use a genuine golden orange board card: confirm whether this fault occurs repeatedly in the original marking table and after the replacement of the marking table. If there is no abnormality after the replacement of the marking table, check the original marking table. If there is a high frequency or repeated occurrence, please contact the after-sales personnel.
2) use the self-made board card: please confirm whether the given signal of each functional pin of the DB25 board card is consistent with the instruction manual. If you confirm that the given signal is normal, please contact the after-sales personnel.
3. No light, no alarm
Answer: 1) use the genuine golden orange board card to confirm whether this fault occurs repeatedly in the original marking table and after the replacement of the marking table. If there is no abnormality after the replacement of the marking table, check the original marking table. If there is a high frequency or repeated occurrence, please contact the after-sales personnel.
2) using the self-made board card, please confirm whether the given signals of each functional pin of the DB25 board card are consistent with the instructions. If you confirm that the given signals are normal, please contact the after-sales personnel.
4. Poor marking effect
Answer: 1) first, confirm whether the output power of the whole machine has decreased. If the power drops and seriously affects the normal use, please contact the after-sales personnel
2) if the power is normal or the power cannot be tested, set the output power ratio to the output of the whole machine about 8-10W, swing the light isolating jumper, and use the ceramic photosensitive film to detect the spot. If the spot rotates with the swing of the jumper, there is a gap in the spot or there are two spots, it is determined that the spot is multi-mode, please contact the after-sales personnel.
5. Power on without marking
Answer: 1) if the genuine golden orange board card is used, confirm whether this fault occurs repeatedly in the original marking platform and after the replacement of the marking platform. If there is no abnormality after the replacement of the marking platform, check the original marking platform. If there is a high frequency or repeated occurrence, please contact the after-sales personnel.
2) if it is a self-made board card, please confirm whether the given signals of each functional pin of the DB25 board card are consistent with the instructions.
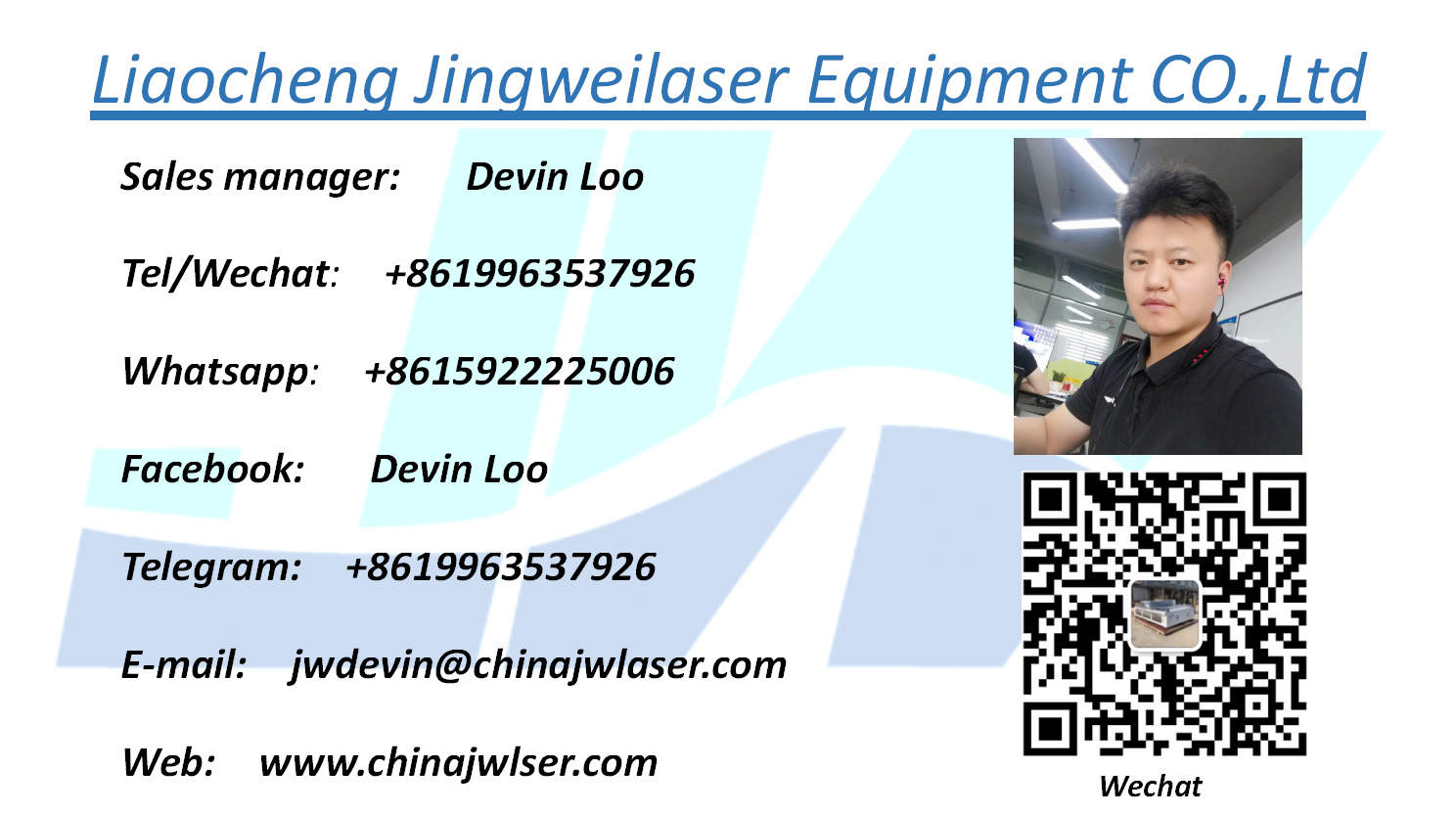
Raycus,laser,source,laser,machine,with,raycus,source,laser,machine
Latest News
CONTACT US
Please Send The Contact Email To
Welcome to inquire
LIAOCHENG JINGWEI LASER EQUIPMENT CO.,LTD
Address:No. 111, Baililai Kechuang Town, Intersection of Hunan Road and Xindonghuan, Liaocheng High-tech Zone, Liaocheng, Shandong, China
Whatsapp:+86-19963537926
Mob:+86-19963537926
MESSAGE